A Task 29 solar system was installed at a coffee drying facility near Sona, Panama. This is part of a totally new development by the recently established Panama Coffee Trading and Export Company. A number of the principals of this company are associated with a large Panamanian company, Café Duran. Over a three year period, approximately 1200 hectares of Robusta coffee plants have been planted and the first major crop was harvested in 2003. The solar system used incorporates an air heating collector (Solarwall®) supplied by Conserval Engineering of Canada. The Solarwall® panel is profiled metal siding perforated with a pattern of small closely spaced slots. Air is heated as it is drawn over the surface of the panels, through the slots and behind the panels before it is ducted to the furnace. The larger system on the lower roof of the Sona installation uses 610 square metres of roof mounted solar panel which preheats furnace supply air. The furnace, which is wood fired, feeds large vertical dryers which reduce the moisture content of the coffee beans from 52% to 11%. The beans are finally stored in a series of silos. The second solar system installed on the high roof, incorporating 225 square metres of Solarwall® panels, preheats air going to the silos. This system is designed to either further reduce the moisture content of the beans or maintain a constant moisture level, depending on the requirements at the time.
A feasibility study prepared prior to the design of the project predicted that the solar system would deliver 2,300 gJ of energy at a collector efficiency of 55% which would supply 28% of the load. This would save 450 – 750 m3 of wood or 95,800 l/yr of propane (it was expected that the facility would eventually shift to propane due to a looming shortage of wood). The calculated payback for the system was 10 – 20 years for wood and 1.5 years for propane. The reason for the wide range for wood is the lack of consistency in both density and moisture content.
The system was monitored during the 2004/05 drying season. Unfortunately due to problems in the field the harvest was much small than anticipated and due to certain construction delays, the drying facility was not fully completed. During this drying season, only one of the two vertical dryers was operating and only one of the three silos was being used. Consequently, the air flow rate through the collectors was much less than the flow rate for which they were designed. However, the collectors performed as predicted for this lower flow rate and it is expected that they will perform as expected once the facility is operating at capacity.
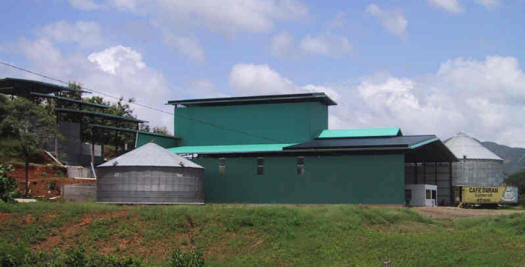
Panama coffee drying facility showing collectors on lower and upper roofs.

Drying silos located next to drying facility.
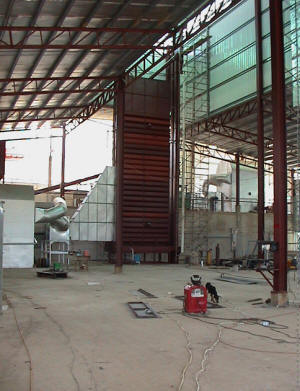
First vertical dryer being installed inside drying facility.